О диагностировании нефтепромысловых труб
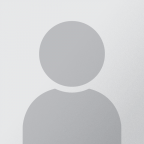
ООО «ПРОМЭКС-Диагностика»:
САДЫКОВ М.А., эксперт в области промышленной безопасности; МИНЕЕВ С.И., эксперт в области промышленной безопасности; ГАРИФУЛЛИН М.М, эксперт в области промышленной безопасности
Номер журнала:
Рубрика:
С технологической точки зрения техническая диагностика трубопроводов включает в себя:
- обнаружение дефектов на трубопроводе;
- проверку изменения проектного положения трубопровода, его деформаций и напряженного состояния;
- оценку коррозионного состояния и защищенности трубопроводов от коррозии;
- влияние трубопроводов на гидрологию трассы и экологию;
- оценку результатов испытаний и диагностики трубопроводов, целесообразность проведения переиспытаний и повторной диагностики;
- интегральную оценку работоспособности трубопроводов, прогнозирование сроков службы и остаточного ресурса трубопровода.
Наиболее эффективным методом неразрушающего контроля является использование внутритрубных дефектоскопов, которые обеспечивают возможность осуществления диагностики на всей протяженности трубопровода. Проблемы возникают, когда по каким-то причинам нет возможности использовать этот метод.
К сожалению, в настоящее время отсутствует полноценная альтернатива внутритрубной диагностики, которая бы позволила осуществить стопроцентную диагностику. Авторами [2] показано, что к нарушению герметизации приводят локальные коррозионные дефекты, далеко не всегда выявляемые при применении какого-либо одного метода диагностики. Поэтому для проведения экспертизы промышленной безопасности или технического диагностирования приходится использовать комбинацию методов.
Авторами [1] показаны преимущества и недостатки отдельных методов неразрушающего контроля, используемые при диагностировании состояния трубопроводов. Ими, в частности, предложена концепция трехэтапного диагностирования объектов, где невозможно использование внутритрубных дефектоскопов.
Первый этап: исследование (сканирование) всей протяженности трубопровода без прямого доступа к исследуемой поверхности и выявление потенциальных дефектов. На этом этапе целесообразно применение сплошного сканирования методами магнитной памяти металла (ММПМ) и УЗ-длинноволнового метода (использование системы Wavemarker).
Второй этап: диагностические работы для подтверждения наличия/отсутствия и определения точного места расположения дефектов, выявленных на первом этапе. Индентификация дефектов методом сканирования поверхности — система TS/PS-2000 или аналоги — для сканирования доступной поверхности трубопровода. Применение данной системы позволяет оперативно проводить ДДК для подтверждения наличия или отсутствия предполагаемых по результатам сплошного сканирования методами ММПМ и Wavemaker дефектов.
Третий этап: определение типа и размера дефектов, подтвержденных на втором этапе. Основной метод на данном этапе — это УЗ-дефектоскопия. Одними из наиболее технически совершенных являются УЗ-дефектоскопы на фазированных решетках.
Наиболее эффективным методом неразрушающего контроля нефтепромысловых труб является использование внутритрубных дефектоскопов, которые обеспечивают возможность осуществления диагностики на всей протяженности трубопровода. Проблемы возникают, когда по каким-то причинам нет возможности использовать этот метод.
Согласно авторам [1] второй и третий этапы по отношению к первому, основному этапу, являются дополнительным диагностическим контролем (ДДК). На этих этапах осуществляется сканирование доступной поверхности трубопровода для выявления и локализации расположения дефектов, выявленных по результатам сканирования всей протяженности, и измерение размеров выявленных дефектов.
Чем точнее удается определить локализацию и характер дефекта, тем больший мультипликативный эффект как с точки зрения экономики, так и с точки зрения безопасности удается достичь. Как указано в работе [3], при диагностировании современными методами неразрушающего контроля участка трубопровода в одной точке доступа (место проведения ремонтных работ) могут быть выявлены дефекты на расстоянии до 10-12 метров в обе стороны. Соответственно, по результатам диагностики может быть принято решение о ремонте не одного километра протяженности трубопровода, а, к примеру, 20-25 м.
В этих целях при планировании мероприятий по диагностированию трубопроводов следует учитывать следующие принципы [1]:
- предусматривать минимум два независимых метода диагностирования в случаях выявления недопустимых дефектов или дефектов, требующих устранения в течение ближайших 2-3 лет;
- в процесс выявления, локализации и идентификации дефектов вовлекать не менее двух специалистов/дефектоскопистов по неразрушающему контролю;
- контрольные процедуры, связанные с количеством и качеством выполняемых работ по диагностированию, выполнять и специалистами специализированной подрядной организации, и экспертами/ кураторами заказчика;
- корректирующие мероприятия в процессе выполнения работ по диагностированию предусматривать на всех этапах диагностирования, связанных с применением различных методов диагностики и экспертизой полученных результатов, с участием специалистов заказчика.
Литература
1. Вагайцев С.Н., Сивоконь И.С. Диагностика нефтепромысловых трубопроводов с применением современного оборудования для неразрушающего контроля. Концепция, лучшая практика, развитие // Территория Нефтегаз. - 2013. — № 8. стр. 28.
2. Внедрение новой концепции диагностики технологических трубопроводов в ОАО «Самотлорнефтегаз» / Галиуллин М.Ф., Шевченко С.Д., Вагайцев С.Н., Левченко А.В., Саража С.В. // В мире неразрушающего контроля. — 2012. — № 3 (57).
3. Сивоконь И.С. Повышение надежности трубопроводов, подверженных локальной коррозии // Территория Нефтегаз. — 2014 год, май. — Стр. 36-43.
4. Аварийность и травматизм на объектах нефтегазового комплекса // Информационный бюллетень Федеральной службы по экологическому, технологическому и атомному надзору. — ЗАО НТЦ ПБ. — 2015 год. — 110 с.
Республика Татарстан, г. Казань, пер. Дорожный, д. 3а (Малые Клыки), а/я 26,
телефон/факс: (843) 203-63-03, 2-957-958, e-mail: promex-kazan@mail.ru, http://www.promex-kazan.ru/