Металлургия форсирует внедрение новаций
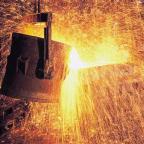
Номер журнала:
Рубрика:
Cогласно отраслевым кодификаторам видов экономической деятельности, предприятия металлургической отрасли входят в подотрасль машиностроения – «металлургическое производство и производство готовых металлических изделий».
По итогам 2010 г., объем выпуска товарной продукции по этой группе составил 36,3 млрд рублей, индекс промышленного производства – 103,1 %. В объеме выпуска товарной продукции предприятиями машиностроительного комплекса, доля металлургических компаний составила 15,6 %. По итогам работы за четыре месяца текущего года металлургическими предприятиями произведено товарной продукции на сумму 12,1 млрд рублей.
Одним из ведущих представителей данной отрасли в Республике Татарстан является ОАО «КАМАЗ-Металлургия» – дочернее предприятие
ОАО «КАМАЗ», объединяющее литейный и кузнечный заводы, с численностью персонала больше 10 тыс. человек. Это одно из тех металлургических предприятий России, которые отличаются своей многолетней историей и высоким профессионализмом кадров. Первые главы летописи заводов написаны еще в 1971 г., во время масштабной стройки автогиганта на Каме. В 2011 г., в июле, литейный и кузнечный заводы пересекут свой сорокалетний рубеж. Металлургическое производство «КАМАЗа» всегда было пионером в применении лучших образцов зарубежной и отечественной техники и технологий.
Подъем, отмечавшийся в докризисные годы, дал возможность металлургам проводить техническое перевооружение производства, вкладывать значительные средства в развитие. И все инвестиционные проекты ориентированы на повышение качества, производительности труда и снижение доли ручного труда в производстве.
Подъем, отмечавшийся в докризисные годы, дал возможность металлургам проводить техническое перевооружение производства, вкладывать значительные средства в развитие. И все инвестиционные проекты ориентированы на повышение качества, производительности труда и снижение доли ручного труда в производстве. Хорошим примером повышения качества и производительности труда за счет внедрения новых технологий и оборудования стал внедренный литейщиками «КАМАЗа» проект технологии ковшового модифицирования чугуна, разработанной фирмой «PROGELTA» (Италия). Уже не первый год стабильный технологический процесс с минимумом человеческого фактора, позволяет получать заданное качество высокопрочного чугуна в каждой отливке и большой экономический эффект. Если еще в 2006 г. в общем объеме продукции из чугуна отливки из высокопрочного чугуна составляли здесь чуть более 40 %, то к концу 2010 г. их объем достиг 55 %.
Другой пример – в том же производстве чугунного литья смонтирован и запущен в работу участок производства стержней методом холодно-твердеющих смесей (Cold-Box процесс). Комплекс представляет собой цепочку специализированного оборудования, его эксплуатация позволяет создать в рамках одного участка целостный технологический поток от приготовления стрежневой смеси до подачи готовых стержней на склад. На сегодняшний день на участке освоено изготовление стержней для производства отливок для четырех- и шестицилиндровых «блоков цилиндров», а также «головок блоков цилиндров».
Одним из ведущих представителей металлургической отрасли в Республике Татарстан является ОАО «КАМАЗ-Металлургия» – дочернее предприятие ОАО «КАМАЗ».
Примером того, как эксплуатация станков может автоматизировать производственный процесс и снизить долю ручного труда, может служить работа двух зачистных станков, речь идет о станках фирм «Maus» и «AutoGrinding LTD». Это оборудование предназначено для обработки отливок «тормозной барабан» и «блок цилиндров». В результате их эксплуатации металлургам удалось, автоматизировать процесс зачистки отливок и снизить долю ручного труда на финишном участке корпуса чугунного литья.
В 2011 г. в «КАМАЗ-Металлургии» запланировано проинвестировать в производство более 150 млн рублей.
В тесном тандеме с технологами заводов работают конструкторы и программисты. Важную роль на предприятии уделяют IT-инновациям. Как один из примеров – закуплена программа моделирования литейных процессов ProCAST (разработчик – ESI group, Франция). Уже не первый год эксперименты при освоении отливок и изменении технологии проводятся на компьютере, пробные варианты «отливаются» виртуально и передаются для таких же, виртуальных, испытаний в Научно-технический Центр
«КАМАЗа». Потенциальный брак устраняется «в зародыше» – без дорогостоящего изготовления заготовки и натуральных испытаний.
И еще один IT-проект позволил металлургам в несколько раз повысить эффективность бизнес-процессов. Речь идет о новой интегрированной системе управления на платформе SAP ERP. Работа над этим IT-проектом началась в 2008 г., результатом его внедрения стала полномасштабная автоматизация всех ключевых бизнес процессов предприятия. И это лишь часть примеров, свидетельствующих о том, что в ОАО «КАМАЗ-Металлургия» в ход идет любое ноу-хау, которое сулит улучшение. За последние годы имеющиеся технологии заметно пополнились новыми интеллектуальными продуктами и служат не только конкурентоспособности предприятия, но и брэнда «КАМАЗ» в целом. И еще важный момент. В «КАМАЗ-Металлургии» постоянно учат персонал уже на своих Lean-учебных и практических курсах.
В планах предприятия – дальнейшая модернизация производства. Например, в ближайшее время основные инвестиции в модернизацию производства для литейного завода связаны с реализацией масштабного проекта по освоению отливки «гильза цилиндра». В связи с этим в производстве чугунного литья (ПЧЛ) будет проведена модернизация автоматической формовочной линии HWS-1. Другой крупный проект – освоением продукции по заказу компании «DAIMLER». В его рамках будет рассматриваться вариант оснащения ПЧЛ новой формовочной линией. В производстве стального литья активно идет модернизация дуговых сталеплавильных печей. А на кузнечном заводе планируется продолжить реализацию проекта «наплавка штамповой оснастки». В текущем году будет закуплена вторая установка для ремонта штамповой оснастки методом наплавки (первая была запущена в эксплуатацию в 2008 г.). Как и в прошлые годы, большое внимание здесь будет уделено освоению проектов в рамках производственной системы. Акцент в этой работе будет сделан на повышение производительности труда, снижение уровня брака и всех видов издержек, сокращение запасов производства.
Важную роль на предприятиях металлургического комплекса Татарстана уделяется IT-инновациям. В тесном тандеме с технологами заводов работают конструкторы и программисты. IT-проекты позволяют металлургам в несколько раз повышать эффективность бизнес-процессов.
Также есть предприятия, которые успешно развиваются в области металлообработки. Например, ОАО «КМПО» обладает большим опытом и современным уровнем технологии, необходимым оборудованием для производства высококачественных отливок способом литья по выплавляемым моделям для жаропрочных сплавов и сталей, литья цветных металлов в кокиль, под давлением, в песчано-глинистые формы, и получать при этом простые и сложные по конфигурации отливки.
Литейный цех ОАО «КОМЗ» применяет в своей работе следующие технологические методы литья: Литье в песчано-глинистые формы (ПГФ), литье под давлением (ЛПД), литье по выплавляемым моделям (ЛВМ), литье пластической штамповкой (ПШ), центробежное литье (ЦБЛ).
ОАО «Зеленодольский завод им. A.M. Горького» имеет развитое машиностроительное производство, располагающее литейным, кузнечным, термическим, гальваническим, сварочным и механообрабатывающим цехами. Это позволяет предприятию самостоятельно производить широкую номенклатуру изделий для нефтегазодобывающей отрасли. Цех титанового литья ОАО «Зеленодольский завод им. A.M. Горького» является одним из крупнейших в мире по производству фасонных титановых отливок для важнейших отраслей промышленности: судостроительной, авиационной, аэрокосмической, нефтегазодобывающей, в том числе для разработки месторождений на морских шельфах.
Завод выпускает и поставляет машиностроительную продукцию по нескольким направлениям. Первое – изделия судового машиностроения, продукция нефтяного и химического машиностроения. Второе – газовое оборудование. Третье – прочая машиностроительная продукция и работы.