Оценка технических рисков и повышение надежности нефтепромыслового оборудования и систем транспортировки нефти в ОАО «Белкамнефть»
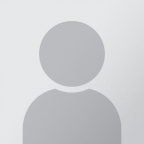
Граханцев Н.М.
главный инженер
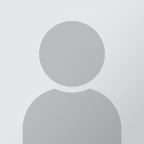
Канюк О.П.
начальник УПиЭБ
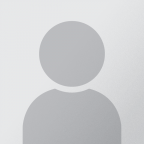
Нагаев Р.Ф.
начальник УДНГ
Номер журнала:
Рубрика:
Обновление основных производственных фондов и повышение ресурса эксплуатируемого оборудования является важнейшей составляющей системы промышленной и экологической безопасности ОАО «Белкамнефть». При этом инвестиционное планирование осуществляется на всестороннем анализе технических рисков.
Технический риск (вероятность отказа технических устройств с последствиями определенного уровня за определенный период функционирования опасного производственного объекта) является одним из основных показателей риска аварии, инцидента или несчастного случая. Анализ риска аварий на опасных производственных объектах (ОПО) является составной частью управления промышленной безопасностью. Результаты анализа риска используются при декларировании промышленной безопасности ОПО, экспертизе промышленной безопасности, обосновании технических решений по обеспечению безопасности, страховании, экономическом анализе безопасности при обновлении основных производственных фондов по критериям «стоимость — безопасность — выгода», оценке воздействия хозяйственной деятельности на окружающую природную среду и при других процедурах, связанных с анализом безопасности.
Диагностика как элемент оценки технических рисков
Контроль и диагностика технического состояния оборудования в процессе эксплуатации является одним из элементов оценки технических рисков. При этом контроль материала деталей и узлов выполняется на собранных конструкциях, как правило, без каких-либо демонтажных работ. Он проводится в процессе использования оборудования. Объем и технология неразрушающего контроля во многом зависят от принятых методов эксплуатации техники. В настоящее время используют следующие методы эксплуатации механизмов, машин, оборудования и других технических объектов: по ресурсу, по состоянию и смешанный.
Технический ресурс — показатель долговечности, характеризующий запас возможной наработки объекта. При эксплуатации по ресурсу для каждого технического объекта устанавливают общую наработку (ресурс) объекта в часах, годах, циклах нагружения и так далее до наступления предельного состояния, после выработки которой объект, как правило, списывают. Определяют также наработку между профилактическими работами, до первого капитального ремонта и между ремонтами. Ремонт выполняется независимо от фактического состояния объекта, хотя объем ремонта от состояния объекта, конечно, зависит и не является заранее заданным. Ряд деталей, узлов и агрегатов заменяют без учета состояния каждого из них.
Здесь, как с экономической, так и с точки зрения промышленной и экологической безопасности, целесообразно внедрение системы индивидуального прогнозирования ресурса, которая позволяет не только предупреждать возможные отказы и непредвиденные достижения предельных состояний, но и более правильно планировать режимы эксплуатации, профилактические мероприятия и снабжение запасными частями. Более того, переход к индивидуальному прогнозированию ведет к увеличению среднего ресурса оборудования, поскольку уменьшается доля конструкций, преждевременно снимаемых для ремонта, и открывается путь для обоснования выбора оптимального срока эксплуатации.
Прогнозирование индивидуального ресурса включает целый комплекс задач: оценка текущего технического состояния объекта, прогнозирование развития этого состояния на ближайшее будущее и выдача на основе этого прогноза рекомендаций об оптимальном остаточном сроке эксплуатации (до списания данного объекта или его очередного ремонта). Если доступной информации недостаточно для вынесения решений о прекращении эксплуатации, то необходимо назначить обоснованный срок очередного диагностирования объекта. Вместе с тем в задачу прогнозирования входит оценка вероятностей наступления различных отказов с целью их предупреждения. Еще одна задача индивидуального прогнозирования — оценка риска по отношению к опасным аварийным ситуациям, установление предельно допустимых остаточных сроков эксплуатации при наличии возрастающего риска и выдача рекомендации о мерах по повышению безопасности.
Сущность эксплуатации по состоянию заключается в том, что наработка объекта не назначается. Не устанавливается также наработка до капитального ремонта, хотя сам ремонт предусматривается и заблаговременно готовится основная технологическая ремонтная документация. Но в большом объеме планируются периодические контрольно-проверочные работы, по результатам которых принимается решение о том, что делать с техническим объектом: допускать его к дальнейшей эксплуатации, подвергать мелкому текущему ремонту с заменой отдельных деталей или агрегатов, либо направлять в капитальный ремонт.
При смешанном методе эксплуатации часть элементов технического объекта эксплуатируется по техническому состоянию, остальное — по ресурсу. Смешанный метод эксплуатации в настоящее время является основным и таким останется в будущем, так как при любом развитии средств контроля невозможно в каждый момент времени точно знать состояние материала всех без исключения деталей и узлов технического объекта. Перевод на эксплуатацию по техническому состоянию и на смешанный метод эксплуатации, как правило, приводит к повышению уровня исправности и надежности техники. Это достигается благодаря внедрению более тщательного контроля значительно большего числа деталей на каждом объекте. В большинстве случаев снижаются также общие эксплуатационные расходы — из-за уменьшения ремонтных работ. Следствием эксплуатации по состоянию является обоснованное увеличение фактического срока эксплуатации оборудования без замены его на новое, что дает значительный экономический эффект. Кроме этого, уменьшаются материальные затраты на возмещение потерь техники, которые происходили бы из-за разрушения ненадежных ее деталей, узлов и конструкций при отсутствии контроля или при контроле в меньшем объеме. При эксплуатации оборудования по состоянию, так же как при других методах эксплуатации, контролируют:
- состояние материала деталей, узлов и конструкций неразрушающими методами;
- работоспособность и функционирование систем методами технической диагностики.
При техническом обслуживании оборудования контроль производят с применением инструментальных средств неразрушающего контроля.
На предприятии успешно внедрен принципиально новый метод диагностики оборудования и конструкций, основанный на использовании магнитной памяти металла. Метод объединяет потенциальные возможности неразрушающего контроля и механики разрушений, вследствие чего, имеет ряд существенных преимуществ перед другими методами при контроле промышленных объектов. Он позволяет выполнить интегральную оценку состояния объекта с учетом качества металла, фактических условий эксплуатации и конструктивных особенностей объекта.
Чаще проверяют высоконагруженные и другие ответственные детали и узлы. При большой наработке в связи с появлением и развитием усталостных и термических трещин, коррозионных и эрозионных поражений и расслоений предусматривается увеличение числа контролируемых деталей, узлов и агрегатов и усиление тщательности и частоты проверок, внедрение комплексного неразрушающего контроля с использованием нескольких дополняющих друг друга методов. Эксплуатационный контроль в основном производят портативными, переносными и передвижными дефектоскопами. Повышение надежности функционирования оборудования достигается применением встроенных систем диагностики наиболее ответственных и нагруженных деталей и узлов.
Повышение ресурса насосных штанг
Для глубиннонасосной эксплуатации скважин при разработке нефтяных месторождений широко применяются штанговые глубинные насосы. Их эксплуатация связана с высоким уровнем технических рисков. Поэтому в ОАО «Белкамнефть» особое внимание уделяется увеличению ресурса элементов штанговых насосов, подвергающихся интенсивной нагрузке.
Еще шесть лет назад ОАО «Белкамнефть» не имело структурного подразделения по ремонту труб и штанг. В настоящее время в составе цеха ПКРС НГДУ-1 в селе Каракулино успешно работает участок по ремонту труб и штанг (УРТиШ), который полностью закрывает потребности предприятия в данном виде ремонта. Это удается благодаря высокому техническому уровню оснащенности, механизации и культуре производства, автоматизированному контролю и современным методам диагностики. Техническими специалистами при поддержке руководства предприятия был начат поиск оборудования, которое бы удовлетворяло современным требованиям промышленной и экологической безопасности и позволило повысить срок службы нефтепромыслового оборудования. Рассмотрели множество самых разных вариантов и предложений, изучили оборудование как отечественных, так и зарубежных производителей.
Выбор был сделан в пользу комплексной технологии упрочнения и дефектоскопии насосных штанг, разработанной ООО «НПИЦ «Качество» (г. Ижевск), и моечного агрегата ОАО «ВНИИТнефть» (г. Самара). В основу моечного агрегата работники института заложили наиболее понятный по своему физическому смыслу принцип: мойка внутренней и наружной поверхности трубы или наружной поверхности насосной штанги горячей водой, без использования моющих растворов, разогретой до 90°С, подаваемой под напором 0,4-0,5 МПа; очистка внутренней и наружной поверхности трубы или наружной поверхности насосной штанги и вынос механических примесей в шламоотстойник. Отработанная вода проходит очистку от легких и тяжелых фракций, дополнительно подогревается и повторно подается на мойку. Моечный агрегат позволяет одновременно производить очистку четырех труб или двенадцати насосных штанг.
Экономические расчеты показали, что моечный агрегат окупится за 1,7 года, а самое главное, люди будут работать в нормальных условиях и не произойдет загрязнения окружающей среды, охрана которой на предприятии ОАО «Белкамнефть» является направлением приоритетным.
Увеличить межремонтный период работы скважин, повысить качество ремонта и поднять производительность труда — над этими задачами не перестают работать специалисты и руководство предприятия. Внедрение в производство нового оборудования и современных технологий дает реальные результаты.
В 2000 году число аварий со штанговыми колоннами в НГДУ-1 ОАО «Белкамнефть» составляло более 200 случаев со средней наработкой на отказ насосных штанг в 9 млн циклов. Основная доля обрывов штанги приходилась на ее тело. Требовалось новое решение по увеличению долговечности насосных штанг, которое позволило бы сократить потребность предприятия в новой штанге. На заводах-изготовителях были изучены дробеструйные установки, упрочняющие тело штанги посредством направленных ударов дробью. Такая технология дает хороший результат, но имеет и ряд недостатков. Оборудование слишком громоздкое и требует регулярного пополнения расходного материала — дроби, поэтому предпочтение было отдано компактному и высокопроизводительному комплексу упрочнения и дефектоскопии насосных штанг отечественного производителя ООО НПИЦ «Качество».
Срок окупаемости составил 6 месяцев. Число обрывов насосных штанг в течение последних четырех лет стабилизировались и составляет около 60-70 обрывов в год. Средняя наработка на отказ насосных штанг превышает 13 млн циклов, хотя в настоящее время только половина всего фонда насосных штанг обработана по новой технологии.
Использование стопроцентного входного неразрушающего контроля тела насосных штанг эхо-импульсным методом сократило отказы на 17 % в период приработки (до 3 млн циклов). Принцип работы акустического дефектоскопа насосных штанг АДНШ отличается простотой. Излучатель и приемник акустических сигналов располагается в едином корпусе и устанавливается на торец насосной штанги. Если считать, что акустический сигнал распространяется со скоростью более 5 тыс. мм в сек., то неразрушающий контроль штанги длиной 9 метров осуществлятся менее чем за 4 сек. Помимо этого не требуется подготовка поверхности для контроля и механическое оборудование для натяжения насосной штанги. Дефектоскоп АДНШ имеет сертификат об утверждении типа средства измерений (RU.С.27.005.А № 26957), регистрацию в Государственном реестре средств измерений под № 34044-07. Повышение долговечности насосных штанг напрямую связано с упрочнением галтели и части тела на участке 300 мм от подэлеваторного бурта.
В 2001 году доля отказов по галтельной части составляла 63% от всех отказов по телу насосной штанги. За 5,5 лет работы в скважине не произошло ни одного отказа насосных штанг как новых, так и бывших в эксплуатации по упрочненной части. Принцип работы установки упрочнения несложен — элементы насосных штанг подвергаются орбитальной обкатке профильными роликами с заданным усилием деформирования. Тело и галтель штанги упрочняются на глубину до 0,2 мм, при этом поверхностные дефекты допустимых размеров «залечиваются». Холодная обкатка профилированными роликами обеспечивает повышение твердости, прочности и циклической долговечности за счет наклепа поверхностного наиболее нагруженного слоя тела штанги и создания в нем сжимающих остаточных напряжений. Кроме того, обкатка профилированными роликами позволяет удалить солевые отложения и окалину механическим способом и резко снизить высоту микронеровностей поверхностного слоя, что упрощает визуальный контроль насосных штанг и препятствует отложению солей и парафина.
Холодная орбитальная обкатка роликами используется не только как метод упрочнения, но и как способ контроля и восстановления насосных штанг. На установке упрочнения бракуется порядка 1 — 3 % насосных штанг. На гладкой, упрочненной, блестящей поверхности после обкатки роликами отчетливо проявляются продольные и поперечные микротрещины и другие, невидимые под слоем солевых отложений и окалины дефекты. Продольные и поперечные микротрещины малых размеров устраняются в результате нейтрализации («залечивания») и не служат концентраторами для развития усталостных трещин.
Просчитав реальную эффективность обновления и модернизации оборудования для сервисного обслуживания насосных штанг, в 2005 году было принято решение об оснащении участка ремонта НКТ дефектоскопом АДНКТ, который аналогичен штанговому. В настоящее время трубам, прошедшим дефектоскопию, присваивается индивидуальный номер, который наносится микроударным методом на тело НКТ. Индивидуальная маркировка труб и штанг позволяет проводить мониторинг нефтедобывающего оборудования, прогнозировать его работоспособность. В будущем планируется продолжить модернизацию оборудования УРТиШ с целью совершенствования технологии ремонта и механизации производственного процесса.
Реконструкция систем измерений количества и показателей качества нефти (СИКН)
В целях обеспечения безаварийной, бесперебойной работы эксплуатируемого оборудования, повышения точности измерений и выполнения требований новых нормативных документов в ОАО «Белкамнефть» ведется работа по реконструкции коммерческих СИКН в части замены эксплуатируемых средств измерений на современные и надежные, приведения в соответствие требованиям вновь вводимых нормативных документов и регламентов ОАО «АК «Транснефть».
В апреле 2006 года введена в промышленную эксплуатацию резервная схема учета нефти СИКН № 607 ПСП «Белкамнефть» с применением массового расходомера ОРТIМАSS и измерительно-вычислительного комплекса ОКТОПУС. Данное решение позволило отказаться от строительства резервуарного парка на территории ПСП, улучшило погрешность измерений массы брутто нефти с ? 0,4 % до ? 0,25 % и полностью автоматизировало процесс измерений.
В 2007 году планируется реконструкция блока качества нефти СИКН № 260 ПСП «Черновское» и СИКН Забегаловского нефтяного месторождения ПСП «Гремиха».
В связи с введением в действие ГОСТа Р 8.615-2005 «Измерение количества извлекаемой из недр нефти и нефтяного газа» ОАО «Белкамнефть» ведет работу по изучению передовых методов и решений по приведению эксплуатируемых на объектах систем измерений в соответствие с требованиями нового национального стандарта. В настоящее время планируется проведение промысловых испытаний измерительного комплекса КТС-ИУ производства ООО «НГС» и комплекта измерительного КИНС производства ООО НПФ «Центрнефтеавтоматика». После получения результатов испытаний будет принято решение о приведении АГЗУ «Спутник» в соответствие с требованиями ГОСТа 8.615 с применением конкретного измерительного комплекта.
Борьба с коррозией
Для предупреждения аварийных ситуаций и повышения срока эксплуатации нефтепромыслового оборудования на объектах ОАО «Белкамнефть» применяются новые современные виды антикоррозионных покрытий. Емкостное оборудование защищается протекторными лакокрасочными материалами, способствующими, помимо барьерной, еще и протекторной защите. Внедряются импортные антикоррозионные материалы известных зарубежных фирм. В системе ППД применяются трубы с внутренним антикоррозионным покрытием, в системе транспорта нефти на наиболее ответственных трубопроводах и на опасных участках — усиленная наружная полимерная изоляция труб. Внедряется система обнаружения утечек «Leak SPY» по волне давления на нефтепроводе между СИКН № 260 ПСП «Черновское» и магистральным нефтепроводом «Ножовка-Киенгоп».
Система обнаружения утечек «Leak SPY» по волне давления предназначена для:
- автоматического определения факта утечек нефти из линейных участков трубопровода;
- определения места нарушения герметичности с заданной точностью (от 100 — 300 м);
- индикации факта и места утечки на мнемосхеме АРМ диспетчера в течение 60 сек.
Применение мультифазной технологии перекачки углеводородов
Традиционные методы транспортировки нефти требуют разделения поступающей из скважины нефтяной эмульсии на составляющие нефть, газ, воду и примеси. В идеале эту задачу наиболее полно решают комплексные установки по подготовке нефти, которые должны быть на каждом месторождении, что является экономически неэффективным. Поэтому, как правило, строятся либо установки предварительного сброса воды (УПСВ), либо дожимные насосные станции (ДНС). При этом попутный газ сжигается на месте, что ведет к его нерациональному использованию и создает дополнительную техногенную и антропогенную нагрузку на окружающую среду.
В целях повышения объемов добычи нефти, полного использования попутного газа, повышения экологической безопасности в ОАО «Белкамнефть» на ДНС Сосновского н.м. внедрена мультифазная технология перекачки углеводородов, которая не требует предварительной сепарации нефтяной эмульсии и обладает рядом неоспоримых преимуществ.
Основной экономический эффект применения мультифазных насосов связан прежде всего с понижением давления на устье скважины, что приводит к увеличению продуктивности. Другой плюс — значительное сокращение количества технологического оборудования на месторождении: вместо компрессоров, однофазных насосов, сепараторов и водоотделителей нужен лишь один трубопровод, по которому идет транспортировка газожидкостной смеси.
Мультифазные насосы обеспечивают уменьшение вредного воздействия на окружающую среду, эффективное использование попутного газа и исключают его факельное сжигание. Кроме того, применение мультифазных насосов увеличивает срок эксплуатации погружных скважинных насосов, дает возможность перекачивать газовые пробки, ведет к снижению эксплуатационных расходов и облегчает контроль за разработкой как новых, так и старых месторождений.
Выводы
Использование новых технологий, модернизация оборудования, обновление основных фондов позволили ОАО «Белкамнефть»:
- исключить допуск к эксплуатации дефектного, с пониженным ресурсом работы оборудования;
- увеличить срок его службы;
- увеличить межремонтный период работы скважин вследствие сокращения числа подземных ремонтов по причине обрывов насосных штанг;
- снизить потери нефти при транспортировке;
- увеличить продуктивность скважин;
- повысить уровень промышленной и экологической безопасности на предприятии;
- получить прирост добычи нефти за счет сокращения числа подземных ремонтов и простоев оборудования.