Автоматизация технологического процесса в блочно-модульных котельных
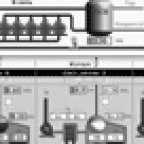
Номер журнала:
Рубрика:
ГОУВПО "Ижевский государственный технический университет" |
Потапов А.Г., магистрант |
Никитин Ю.Р., доцент кафедры "Мехатронные системы" |
В статье показана и обоснована целесообразность применения блочно-модульных котельных с системой автоматизированного управления на технологическим процессом. Автоматизация процесса управления реализована на базе модульной концепции на двух уровнях. Нижний уровень системы управления построен на программируемых логических контроллерах Siemens S7-200 с программированием на языке STEP 7 c человеко-машинным интерфейсом на базе Simatic WinCC flexible. Верхний уровень системы управления реализуется посредством SCADA-системы на персональном компьютере.
Развитие технологии автоматизации производственных процессов привело к тому, что современная котельная представляет целую совокупность разнообразнейших технических приспособлений, предназначенных для контроля и управления рядом физических процессов, общей целью которых является преобразование потенциальной энергии сжигаемого топлива в тепловую энергию и передача ее потребителю. К таким процессам относятся сжигание и подача топлива, которым может быть как газ, так и мазут или дизельное топливо; нагрев и транспортировка теплоносителя, которым может быть как пар, так и вода, удаление продуктов сгорания. Необходимо иметь устройства, автоматически прекращающие подачу топлива к горелкам при следующих ситуациях:
• повышении или понижении давления газообразного топлива перед горелками;
• понижении давления жидкого топлива перед горелками, кроме котлов, оборудованных ротационными горелками;
• понижении давления воздуха перед горелками для котлов, оборудованных горелками с принудительной подачей воздуха;
• уменьшении разрежения в топке;
• погашении факелов горелок, отключение которых при работе котла не допускается:
• повышении температуры воды на выходе из котла;
• повышении или понижении давления воды на выходе из котла;
• уменьшении расхода воды через котел;
• неисправности цепей защиты, включая исчезновение напряжения, только для котельных второй категории.
По согласованию с заказчиком данный перечень дополняется в каждом отдельном случае, в частности, практически всегда является обязательным устройство охранно-пожарной сигнализации и датчиков загазованности помещения оксидом углерода (СО) и метаном (СН4).
Краткая характеристика технологического процесса
Процесс управления котельной заключается в следующем: контроль вышеупомянутых параметров и приведение в действие электромагнитных клапанов безопасности при их аварийных значениях, регулирование температуры воды в подающем трубопроводе в зависимости от температуры наружного воздуха посредствам управляемого электроприводом клапана, регулирование объема сжигаемого топлива в зависимости от количества передаваемого тепла.
На рисунке 1 изображена одна из распространенных тепломеханических схем котельной, служащая для обеспечения потребителя горячей водой и отоплением. Основными наименованиями оборудования и материалов данной схемы являются:
1. Два водогрейных котла, в которых происходит сжигание топлива и нагрев воды;
2. Насосы:
2.а. Сетевые, обеспечивающие постоянный перепад давления воды в системе отопления и во внутреннем контуре котельной – между теплообменниками и котлами;
3.б. Циркуляционные насосы контура горячего водоснабжения, обеспечивающие постоянный перепад давления воды в контуре горячего водоснабжения;
3.в. Насос рециркуляции, обеспечивающий поддержание постоянного давления воды перед котлами за счет перемещения нагретой воды, прошедшей через котлы, на участок трубопровода с более холодной водой перед котлами, прошедшей контур отопления и теплообменники;
4. Теплообменники, служащие для нагрева воды;
5. Электроприводы клапанов:
5.а Регулирующий температуру воды в контуре горячего водоснабжения;
5.б Регулирующий температуру воды в контуре отопления;
5.в Компенсирующий потери воды в контуре отопления;
6. Датчики:
6.а ТЕ – датчики температуры, измеряющие и передающие текущее значение температуры контроллеру;
6.б РЕ – датчики давления, измеряющие и передающие текущее значение давления контроллеру;
7. Показывающие приборы:
7.а ТI – термометры, служащие для измерения температуры и проверки правильности работы датчиков;
7.б PI – манометры, служащие для измерения давления и проверки правильности работы датчиков;
8. Расходомеры, служащие для учета израсходованной тепловой энергии;
9. Трубопроводы:
9.а Т1 – подающий трубопровод контура отопления;
9.б Т2 – обратный трубопровод контура отопления;
9.в Т3 – подающий трубопровод контура горячего водоснабжения;
9.г Т.4 – обратный трубопровод контура горячего водоснабжения;
9.д Т95, Т96 – трубопроводы отвода конденсата.
На рисунке 2 изображена схема управления котла, обеспечивающая подачу и управление процессом сжигания топлива – газо-воздушной смеси, отвод дымовых газов, нагрев воды в котле, регулирование разряжения в топке котла, контроль параметров протекающих процессов. Основными наименованиями оборудования данной схемы являются:
1. Котел;
2. Горелочное устройство:
2.а Непосредственно корпус горелки;
2.б Газовый патрубок с соответствующей арматурой;
2.в Воздушный патрубок с соответствующей арматурой;
2.г Микропроцессорный блок управления процессом горения;
2.д Комплект датчиков давления воздуха, давления газа, пламени запальника и факела горелки;
3. Узел учета газа;
4. Трубопроводы:
4.а Вышеупомянутые подающий и обратный трубопроводы Т1 и Т2;
4.б Дымоход котла;
4.в Газоход котельной;
5. Датчики давления и температуры TE, PE;
6. Манометры и термометры PI, TI.
Рис.1 Тепломеханическая
схема котельной
Существует большое количество схем управления всем вышеперечисленным оборудованием: от релейного до микропроцессорного, но современные тенденции развития систем автоматизированного управления технологическими процессами предполагают интеграцию управляющей аппаратуры. Большому количеству контроллеров, каждый из которых отвечает за управление отдельного узла – группы насосов, электроприводов клапанов или аварийных параметров среды, предпочитают один, более мощный, управляющий данными процессами и, кроме того, позволяющий осуществлять передачу данных о состоянии котельной на расстояние и производящий дистанционное управление. Помимо процессов объединения управляющей аппаратуры внутри котельной, все более и более актуальной становится концентрация операторского и обслуживающего персонала в одной точке – диспетчерском пункте, который осуществляет управление и обслуживание всех котельных в определенном радиусе. Все вышеперечисленные меры дают ряд неоспоримых преимуществ за счет очевидной экономии человеческих ресурсов и сокращения аппаратно-технических средств.
Система централизованного контроля
Исходя из целей обеспечения высокого качества воспроизводимого теплоносителя, надежного функционирования технологического оборудования и повышения экономических показателей, была разработана система централизованного контроля котельной. Для этого была разработана SCADA–система.
Основными задачами системы централизованного контроля являются:
• мониторинг технологических параметров работы блочно-модульных котельных;
• автоматическое управление исполнительными механизмами при изменении количества потребляемой энергии и аварийных ситуациях;
• передача данных о состоянии протекающих процессов в котельной на компьютер в помещении оператора;
• возможность формирования на сервере базы данных с параметрами протекающих процессов;
• выдача данных о технологических параметрах текущего процесса выработки тепла на экране отображающего устройства – сенсорной панели, установленной непосредственно в щите автоматики котельной;
• передача предупредительных сигналов при возникновении предаварийных ситуаций;
• возможность выполнения всех вышеперечисленных функций одновременно на нескольких объектах под контролем всего одного диспетчера без снижения критериев качества.
Модульная концепция построения системы
Современные тенденции развития производства предполагают модульную концепцию построения системы, которая реализуется следующим образом.
Нижний уровень системы спроектирован так, что в каждом блок-боксе устанавливается свой щит управления, в котором размещается контроллер, средства визуализации и управления, коммутационная аппаратура. Таким образом, процесс управления оборудованием внутри одного блок-бокса может осуществляться автономно. Подавляющая часть прокладки силовых и контрольных проводников осуществляется в пределах данного блок-бокса, что позволяет сделать это непосредственно на предприятии – изготовителе котельной. За счет этого транспортировать котельную можно с подключенным оборудованием, что также позволяет значительно снизить затраты на командировочные расходы электромонтажников. Близость размещения управляющей аппаратуры к средствам измерения и электродвигателям обуславливает экономию силовых и контрольных кабелей, а также затраты на их прокладку. При попытке реализации модульной концепции системы управления с единым пультом или щитом неизбежно возникновение клеммных коробок на стыке блок-боксов, что значительно снижает надежность данной системы. Наличие идентичных щитов управления позволяет использовать при необходимости их частичную аппаратную и программную взаимозаменяемость, что также позитивно сказывается на качестве процесса управления.
Верхний уровень системы управления реализуется посредствам SCADA–системы. Дистанционно осуществляется управление рядом котельных, создание архивов, аварийная сигнализация. В той или иной степени процесс управления различными котельными совпадает, что позволяет копировать участки уже отработанной программы. При определенной доработке монитор реального времени диспетчерского пункта может быть установлен на нескольких компьютерах или размещен в интернете, что также обеспечит его взаимозаменяемость. Управление рядом котельных из одной точки позволяет значительно снизить затраты на заработную плату обслуживающего персонала, так как один диспетчер может контролировать параметры работы множества объектов, имея в своем распоряжении один компьютер, коммуникационный аппарат, специализированное программное обеспечение.
Аппаратная реализация системы
Рассмотрим аппаратную реализацию системы управления блочно-модульными котельными на примере одной паро-водогрейной котельной, выработка горячей воды систем отопления и горячего водоснабжения которой, а также пара производится при помощи водогрейных КВ-Г и паровых котлов ICI AX-200, оснащенных различным вспомогательным оборудованием и средствами автоматизации.
Система централизованного управления блочно-модульной котельной построена на базе промышленных программируемых контролеров Siemens серии S7-200, является распределенной и состоит из нескольких подсистем. Щит управления водогрейным котлом №1 управляет вспомогательным оборудованием водогрейного котла №1, электродвигателями, приводами, анализирует показания датчиков, расположенных в данном блок-боксе; щит управления водогрейным котлом №2 выполняет аналогичные функции для водогрейного котла №2; щит управления водогрейным котлом №3 – аналогичные функции для водогрейного котла №3 и, кроме того, дистанционную передачу сигналов посредствам GSM (GPRS)–модема. Щит автоматики осуществляет координацию работы двух паровых котлов и визуализацию параметров работы всей котельной на сенсорной панели; щиты управления паровыми котлами №1 и №2 поставляются комплектно с котлами и отвечают за управление оборудования, входящего в комплект поставки котла, имеют в своем составе ПЛК. Связь подсистем осуществляется по протоколу RS-485. Выбор протокола передачи данных был обусловлен длиной кабеля, соединяющего щиты управления (не превышает 30 м), а также наличием 2-х встроенных в контроллер портов RS-485.
Кроме того, каждый котел укомплектован газо-горелочным устройством фирмы Unigas, которое, в свою очередь, оснащено встроенными менеджерами горения, представляющими собой микропроцессорный блок с фиксированной логикой. Основная функция менеджера горения заключается в выполнении локальной задачи автоматизации – процесса сжигания топлива. Для того чтобы процесс сжигания газа был безопасным и рациональным, менеджеру горения необходимо осуществлять следующий перечень управляющих воздействий: регулирование соотношения сжигаемой газо-воздушной смеси, в том числе управление приводом газового дросселя, регулирование частоты вращения дутьевого воздушного вентилятора; контроль давления газа, контроль давления воздуха, контроль пламени запальника, контроль герметичности газовых клапанов, осуществление циклов продувки и розжига горелки, измерение температуры воды после котла и поддержание ее постоянного значения при помощи регулирования мощности горелки.
Контроллер, находящийся в щите, собирает данные со всех датчиков, обрабатывает их, сохраняет в блоке данных для последующей передачи в базу данных. Нижний уровень аппаратуры управления представлен датчиками температуры горячей воды; датчиком температуры пара в паропроводе и окружающем воздухе (термопреобразователи сопротивления Pt100), датчиками температуры дымовых газов, (термосопротивление Pt500), датчиками давления воды с аналоговым сигналом, с дискретным сигналом; давления газа, давления пара, датчиками уровня жидкости.
Применяемые программные средства
Программирование контроллера производится с помощью программного пакета STEP 7 v.5.3. Система централизованного контроля использует SCADA-систему MasterScada, которая в силу своей абсолютной открытости легко взаимодействует со стандартными и пользовательскими программами, решает задачи визуализации.
Система диспетчеризации осуществляет информационное обеспечение оперативного персонала специалистов и руководителей, позволяет своевременно предупреждать и выявлять аварийные ситуации, обеспечивает формирование отчетных документов непосредственно на рабочих местах специалистов, снизить количество обслуживающего персонала и соответственно затраты на его содержание.
Рис.2 Схема управления котла
Состав и структура системы диспетчеризации: распределенная двухуровневая система. Нижний уровень, разрабатываемый в среде STEP 7 v.5.3, предназначен для сбора и первичной обработки информации с датчиков, построен на контроллерах. С них на верхний уровень передается текущая и архивная информация. Технические средства первого уровня - датчики, контроллеры и средства передачи информации - размещаются в помещениях котельных. Технические средства первого уровня каждой котельной образуют отдельную подсистему, обеспечивающую также автономную работу. При восстановлении связи с верхним уровнем накопленная за время автономной работы архивная информация автоматически передается на верхний уровень.
Для реализации системы человеко-машинного интерфейса нижнего уровня было использовано программное обеспечение SIMATIC WinCC flexible, предназначенное для решения обширного комплекса задач: от разработки проекта отдельно взятой панели оператора до разработки мощных систем человеко-машинного интерфейса с архитектурой клиент/сервер. WinCC flexible обеспечивает возможность разработки проектов для всех типов панелей оператора на базе Windows. WinCC flexible может работать под управлением операционных систем Windows 2000 Professional/ 2000 Server/ XP Professional и характеризуется следующими показателями:
• поддержка сквозной разработки проектов различной степени сложности; наглядный интуитивно понятный интерфейс, существенно повышающий эффективность выполнения проектных работ;
• использование Web-технологий для обеспечения доступа с одной панели оператора или SIMATIC PC к данным другой, дистанционного обслуживания, наблюдения, диагностики, загрузки проектов;
• поддержка текстовых библиотек для многоязычных текстов;
• поддержка функций эмуляции работы проектов для всех панелей оператора на базе Windows CE, а также компьютерных систем визуализации на основе SIMATIC WinCC flexible Runtime;
• поддержка проектирования коммуникационных соединений и определения параметров передачи данных;
• включение HMI-станций в проекты STEP 7. Просмотр HMI-объектов в дереве STEP 7;
• сокращение затрат на обучение персонала;
• поддержка аналоговых сообщений и свободно конфигурируемых классов сообщений;
• расширенные коммуникативные возможности для управления, сервиса и диагностики;
• обмен данными с одновременной поддержкой нескольких коммуникационных протоколов;
• дистанционное управление, диагностика и администрирование;
• событийная пересылка сообщений по каналам электронной почты;
• поддержка специализированных HTML страниц, соответствующих конкретным типам приборов SIMATIC HMI;
• HTTP связь с другими SIMATIC HMI системами.
SIMATIC WinCC flexible в данном объекте предназначен для конфигурирования микропанели оператора SIMATIC TP177 Micro, встроенной в щит автоматики.
Рис.3 Мнемосхема
котельного оборудования
Второй уровень (верхний) построен на базе персонального компьютера и предназначен для сбора информации с первого уровня, ее обработки, формирования архивов и отчетных документов, представления информации персоналу. Верхний уровень включает в себя АРМ диспетчера (компьютер в промышленном исполнении), на базе которого реализованы серверные функции. АРМ диспетчера подключается к локальной сети предприятия для обеспечения возможности доступа к базе данных со стороны рабочих мест специалистов. Технические средства второго уровня размещаются в помещении центрального пульта управления. Для больших распределенных систем функции АРМ диспетчера и сервера могут быть разделены между различными компьютерами, в системе может быть несколько серверов.
Для предоставления информации на рабочие места специалистов на них устанавливаются Master SCADA (для оперативной технологической информации) и Microsoft Excel (для формирования отчетных документов).
Система является расширяемой, позволяет подключать новое оборудование котельной, а также служит для включения абсолютно новых объектов диспетчеризации, не запланированных изначально, может быть использована и для диспетчеризации отдельных узлов учета и т.п.
Результаты внедрения АСУ ТП в блочно-модульных котельных
В данной работе были реализованы две концепции построения систем автоматизации, отвечающие современным тенденциям развития данной отрасли производства. Это концепция централизованного контроля информации и концепция модульного построения системы.
При внедрении концепции централизованного контроля информации были получены следующие преимущества:
• повышение надежности работы котельных за счет улучшения оперативности обработки информации, поступающей из котельных;
• возможность протоколирования и архивирования информации, анализа работы операторов и оборудования, разбора аварийных ситуаций на основании архивных данных;
• улучшение условий труда обслуживающего персонала;
• снижение затрат на энергоносители при оптимальном регулировании поддерживаемых параметров;
• снижение эксплуатационных затрат и сокращение обслуживающего персонала;
• возможность установки и с необходимой точностью поддержания требуемой температуры воды, что позволило повысить качество продукции.
Относительно модульной концепции построения системы можно сказать, что размещение локальной коммутационной и управляющей аппаратуры в пределах одного блок-бокса позволило получить следующие преимущества:
• снижение затрат на монтаж контрольных и силовых проводников;
• возможность производить подключение оборудования непосредственно на заводе-производителе блочно-модульной котельной, что позволяет транспортировать котельную с более высокой степенью готовности до места назначения;
• повышение надежности работы котельной за счет внедрения в систему управления надежных и взаимозаменяемых комплектующих.
![]() |
Машинников Сергей Николаевич, главный инженер Завода котельного оборудования ООО "Энергетическая Компания «ЭНКО» |
Энергетическая Компания «ЭНКО» занимается производством водогрейных котлов и блочно-модульных котельных уже на протяжении 8-ми лет. В условиях все более и более возрастающих требований Ростехнадзора к процессу эксплуатации котельных установок и повышения необходимости экономии энергетических и людских ресурсов, внедрение автоматизированных систем управления технологическими процессами (АСУТП) котельных становится чрезвычайно актуальным. В «ЭК «ЭНКО» также ведется разработка проектов с использованием АСУТП котельных, позволяющих их эксплуатацию на качественно новом уровне – работу котельной без постоянного обслуживающего персонала с достаточно высокой степенью надежности. Данные концепции были реализованы на нескольких последних объектах, построенных нашей компанией - крышная котельная 1,6 МВт в жилом доме по ул. Коммунаров в г. Ижевске, пристроенная котельная 1,2 МВт по ул. Родниковой, котельная ремонтно-механического завода 6,5 МВт в г. Межгорье - и уже зарекомендовавших себя с хорошей стороны.
![]() |
Редкозубов Виктор Викторович, начальник отдела по надзору за оборудованием, работающим под давлением, и теплоснабжением Управления Ростехнадзора по УР |
Автоматизация и оптимизация технологических процессов получения тепловой энергии позволяет существенно увеличить коэффициент полезного действия энергоустановок.
Все это делает блочно-модульные котельные весьма привлекательными для использования в хозяйственной деятельности на предприятиях всех форм собственности.
Высокие технологические возможности современной цивилизации позволяют оборудовать котельные надежнейшими средствами автоматики и контроля. Это бесспорный плюс.
Однако эксплуатация блочно-модульных котельных имеет свою специфику. Например, затраты на содержание и обслуживание могут не только уменьшаться, но в отдельных случаях и возрастать.
Это происходит по следующим причинам. Во-первых, в состав обслуживающего персонала входят не только операторы дежурных смен, но и аварийная бригада, а также высококвалифицированные специалисты, осуществляющие обслуживание, диагностику, ремонт и наладку систем автоматизации и контроля.
Подготовка и содержание такого персонала будет стоить недешево. Во-вторых, в отдельных регионах или населенных пунктах просто может не оказаться специалистов такого уровня. В этом случае заключение договоров на обслуживание с организациями из других регионов или местностей потребует дополнительных затрат. В-третьих, в условиях сурового климата нашей страны, а также в связи с усиливающейся угрозой террористических актов необходимо принимать в расчет возможные перебои в подаче газа и учитывать возможность использования в технологической цепи альтернативных видов топлива и создание в необходимых количествах его запасов.
В большинстве блочно-модульных котельных в качестве резервного топлива используется дорогостоящее дизельное топливо, так как использование мазута требует больших трудозатрат по содержанию мазутного хозяйства;
В-четвертых, при присоединении к одному газопроводу нескольких котельных, информация о работе которых поступает на один диспетчерский пункт, при аварии или снижении давления газа на газопроводе может произойти автоматическое закрытие ПЗК на нескольких котельных. В этом случае время, необходимое аварийным бригадам на восстановление теплоснабжения, увеличится, а в условиях низких температур это может привести к серьезным последствиям. Для дистанционного запуска котельных с диспетчерского пункта необходима установка телемеханики.
Кроме того, если большая теплоэнергетика имеет свои традиции, богатый, накопленный десятилетиями опыт, мощную структуру производственного обучения и производственного контроля за безопасной эксплуатацией оборудования, то всего этого, конечно же, нет на каком-либо малом предприятии, пожелавшем в целях экономии обогреть свой офис при помощи котельной блочно-модульного типа, хотя и с высокой степенью автоматизации технологического процесса.
Вдобавок ко всему, заказчик, выдающий технические условия на поставку или проектирование, зачастую бывает некомпетентен и при покупке руководствуется только принципами экономии, а в результате получает товар некомплектный, неудовлетворяющий требованиям обязательной к исполнению нормативно-технической документации.
При допуске таких котельных в эксплуатацию начинаются проблемы, и не малые. Появляются непредвиденные расходы, во много раз превосходящие полученную «экономию».