Автоматизация качества
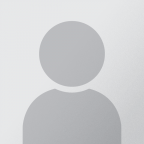
Номер журнала:
Рубрика:
Оборудование и трубы, производимые для предприятий нефтяного комплекса, в настоящее время должны соответствовать более высоким качественным характеристикам, которые, в том числе, способствуют снижению промышленных и экологических рисков. Опыт внедрения современных технологий в данном сегменте освоен в ООО «НПО «ЗНОК и ППД».
![]() |
Хусаинов Радик Робертович, исполнительный диретор по управлению ООО «НПО «ЗНОК и ППД» |
Научно-производственное объединение «ЗНОК и ППД» - предприятие с высоким техническим и технологическим потенциалом, специализирующееся на производстве труб и фасонных изделий в антикоррозионном и теплоизолированном исполнениях, экспертном обследовании нефтепромыслового оборудования, диагностировании трубопроводов и других объектов.
Благодаря использованию современного оборудования, прогрессивных технологий и материалов, а также многолетнему опыту работы предприятие выпускает продукцию, отвечающую высоким требованиям надежности, долговечности и экологической безопасности.
Профессионализм сотрудников НПО обеспечивает надлежащий уровень сервисных услуг и гарантирует квалифицированную помощь и консультации по самым разнообразным вопросам антикоррозионной защиты, восстановления труб и нефтепромыслового оборудования.
Модернизация цеха №1
В целях повышения качества, улучшения основных технологических характеристик производимых на предприятии труб в ООО «НПО «ЗНОК и ППД» была осуществлена работа по модернизации цеха №1.
Ранее на предприятии технология изоляции наружной поверхности труб больших диаметров существовала как дискретное (поштучное) производство, то есть каждую трубу изолировали отдельно. В связи с этим возникала необходимость выполнения множества подготовительных и промежуточных операций для каждого процесса, а именно, для сушки, очистки, нанесения покрытия, и охлаждения трубы. Отсюда - низкая производительность линии. При этом применяемое оборудование требовало использования в основном ручного труда для настройки линии в зависимости от геометрии (диаметр и длина) каждой трубы. Соответственно промышленная безопасность, условия труда и культура производства были на низком уровне.
Таким образом, для повышения производительности, улучшения качества, автоматизации и механизации производства было принято решение о модернизации цеха №1. С этой целью было воплощено множество новых технических идей. Для увеличения производительности требовалось исключить необходимость подстраиваться под каждую трубу индивидуально. Возникла необходимость организовать движение труб непрерывным потоком. В связи с этим была разработана и внедрена на линии автоматизированная система движения потока труб (транспортная линия, автоматические перекладыватели, участки отгона и ускорения труб в потоке, датчики заполнения стеллажей). Транспортную линию изготовили из армированных резиновых бандажей Continental, которые позволяют производить точную настройку режимов подачи труб и компенсировать линейные неровности поверхности труб. Для обеспечения высокого качества очистки наружной поверхности труб произведена реконструкция дробеметной установки и участка подготовки труб перед очисткой (грубая очистка, предварительный нагрев поверхности труб). В целях увеличения качества наружного полимерного покрытия (НПП) и значения адгезии непосредственно перед участком нанесения установлена камера обеспыливания поверхности труб, после камеры транспортная линия выполнена из колес с полиуретановым покрытием (при транспортировке труб резиновые колеса в процессе трения о сталь имеют свойства оставлять микроскопические загрязнения - производственную пыль, частички резины, не обнаруживаемые при визуальном осмотре, в профиле шероховатости на поверхности металлов полиуретан таких загрязнений не оставляет). Участок нанесения НПП оборудован блоком экструдеров, прикатывающими роликами, двумя узлами нагрева труб, установкой обеспыливания и установкой нанесения праймера. Для нанесения полимеров (адгезива и полиэтилена) применяются 2 экструдера, установленных на подвижную площадку для возможности их продольной и поперечной настройки относительно движения потока труб. Формирование полимерного полотна осуществляется в плоскощелевых головках экструдеров. Для настройки положения плоскощелевых головок экструдеров в зависимости от наружного диаметра изолируемых труб (от 426 до 1420 мм) разработана и внедрена на линии новая система настройки плоскощелевых головок.
Важную роль в процессе нанесения полимеров играют прикатывающие ролики, от их работы зависит качество и товарный вид продукции. В связи с этим была разработана и внедрена отдельная система настройки геометрии положения, угла атаки и усилия прижатия прикатывающих роликов. Для обеспечения качественного и эффективного охлаждения потока труб с НПП была изготовлена водяная шахта с форсунками. Форма фаски покрытия на трубах обеспечивается специальным блоком обработки фасок. Для проведения качественного контроля труб с НПП организован участок технического контроля, позволяющий проверять толщину, адгезию, диэлектрическую сплошность, ударную прочность и т.п.
Уровень механизации производственной линии в целом значительно снижает воздействие человеческого фактора на всех технологических операциях, что, в свою очередь, уменьшает вероятность выпуска брака и снижает уровень производственных рисков. Системы автоматизации позволяют контролировать процесс (температурные режимы, силовые нагрузки, движение труб по линиям и стеллажам, системы предупреждающих сигнализаций и т.п.) на всех стадиях, при этом количество задействованного персонала не увеличивается.
Республика Татарстан, г. Бугульма, ул. Нефтяников, 5, тел. (85594) 7-20-18, e-mail:znokippd@tatneft.ru